

To have this done seamlessly, an ethernet switch was used.
#Automatic wire stripping machine update#
Ethernet Switch: Multiple components are required to have continuous communication between them to update each other.
#Automatic wire stripping machine manual#

We found that multiple electrical components were required. To solve this problem we looked at similar applications of running stepper motors. For this application, we need to be able to send pulse and direction signals from our Siemens PLC to control when and what motor are enabled, how many steps they need to take, and what direction those steps are being taken. One NEMA 23 high-torque motor for the puller, one for the ejector, and a NEMA 17 low-torque motor for the cutter. First, movement of the machine is driven by three stepper motors. When the insulation is cut, the puller or ejector then pulls on the wire, as the cutter blades stay in place, to expose the stranded core. For cutting, the cutter goes all the way through the insulation and stranded metal core, but for stripping only the insulation needs to be cut. Its assembly was pulled off of a milling machine and is actuated by a NEMA 17 stepper motor and ball screw. Pretty self-explanatory, the cutter is used to cut and strip the wire. Again, springs were used to pull the two parts of the wire straightener together, applying pressure to and straightening the wire. To solve this problem, a wire straightener was made. Wire coming off a spool can be bent, possibly causing problems for the puller and ejector assemblies. These assemblies took the most time design and fabricate mainly due to them being the heart of the process. The ejector on the other hand, is used to either eject cut wire from the machine or position the wire back into the cutter for back-stripping. The puller is used to pull and meter wire off of the spool and to feed rest cutter. Springs, located at the either ends of the assemblies, are the main driving forces that pulls the rollers together giving them the "pinch" needed to pull the wire.Įven though the assemblies are the same, they are used to do different processes. Both pinch roller assemblies are made up of multiple 3D printed and mechanical parts that were either designed or fabricated to work with each other. Very similarly to the EcoStrip 9380, our puller and ejector use motor-controlled pinch rollers to pull the wire off of its spool and feed the rest of the machine. This can be broken down into three parts: the puller and ejector, wire straightener, and cutter.įirst, would be the puller and ejector. Now that we understand what the project is, what we want it to do, and what parts we have to make it happen let's talk about the overall design. Be able to select the length of wire, length of the strip, and number of cut wires.Allow user to control machine manually or automatically through HMI.Strip wire at multiple lengths (depending on ferrule).Cut wire at multiple lengths (min: 5 inches max: 5 feet).Pull, cut, and strip multiple gauges of wire (18 - 14 awg) off of a spool.With these ideas in mind the machine should be able to do the following:
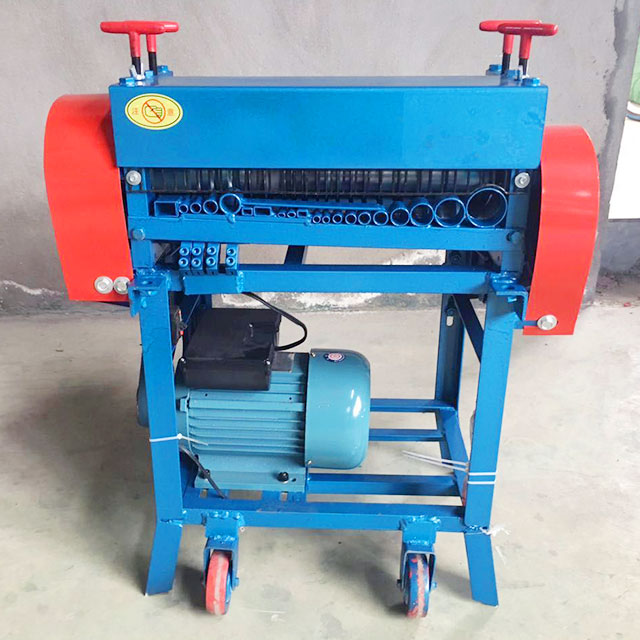
These two aspects combined was the inspiration for this machine. There are plenty of examples out there ranging from hobby types to industrial standard designs, for example, the Scheulniger EcoStrip 9380. To solve this problem, at least cutting and stripping, we created a machine to automate the process. For this project, we decided to automate the process of cutting and stripping wire.įor those who know, the process of cutting, stripping, and feruling wire in electric panels can become tedious, especially when running wire to PLCs. The goal of the Capstone is to be a cumulation of the skills we gained while in class and industry. During our time there, we have been able to learn about mechanical and electrical design, fabrication, and application within industry. We are current sophomores studying Electromechanical Technology at Thaddeus Stevens of Technology. This is a project my team and I made as our final Capstone project. Hello and Thank You for Viewing this Project!Īdam Lueders, Chris Habowski, and Vanessa Penaloza
